How to change a bearing on an Ardo washing machine
In 99% of cases, noise, squeaking and knocking during washing disappears after replacing the bearings in the washing machine. Otherwise, the problem will increase, each cycle will be accompanied by a strong roar, and soon the machine will completely fail, requiring expensive repairs. Therefore, it is better not to take things to extremes and replace the bearing assembly at the first sign of failure. We’ll tell you in detail how to do this quickly and competently, using the Ardo washing machine as an example.
Let's disassemble the machine
The process of replacing the unit is quite labor-intensive, since you can only get to the bearings by pulling out the tank and drum. To do this, you will have to disassemble the machine almost entirely, which often scares away home craftsmen. But in fact, by acting consistently and carefully, anyone can cope with the task. The main thing is not to deviate from the following instructions:
- disconnect the machine from all communications, power supply, water supply and sewerage;
Attention! Don’t forget to record the location of the wires connected to the camera parts to avoid errors during reassembly.
- provide free access to the rear wall of the machine;
- unscrew the corresponding bolts and remove the rear panel;
- remove the belt (in older Ardo models it is V-belt);
- reset the sensors attached to the tank by prying up the rubber bands with a flat screwdriver and bending each group of wires;
- remove the grounding from the shaft by unscrewing the nut at the base;
- release the wiring on the heating element, loosen the bolt holding the heating element, push the rod inward and remove the part;
- unscrew the two screws on top and lift the front panel up from the back;
- take the head 13 and remove the metal plate intended for tightening the tank;
- fix the flywheel with a screwdriver, unscrew the central nut and remove it;
- Unscrew all the screws located at the middle circular joint of the tank;
- grab the top tank with both hands and, moving it in different directions, pull it out through the existing hole.
If you act in this way, there will be no need to remove the counterweights, engine, shock absorbers, dispenser and other untouched elements of the machine. Only the drum with less than half of the tank is pulled out. We place it on an old car tire and begin dismantling and subsequent replacement.
Removing Old Bearings
Having placed the removed tank in front of you, you need to assess the condition of the shaft. Most likely, over many years of use, a lot of rust and scale has accumulated in the center of the casing, so you will have to treat it with a universal cleaner like WD-40. While the composition eats away the dirt, we place a brick base under the container, and a soft pillow between them. We continue to act.
- We knock out the stuck shaft, for which we substitute a rubber mallet and tap it with a hammer until the drum falls inside.
- We knock out the outer bearing and oil seal remaining on the tank.
- If the outer bearing is very stuck, sharpen the chisel and, varying the angle of inclination, knock it out with a hammer.
- When the inner ring is also inaccessible, carefully make cuts on both sides with a grinder and unscrew it with a gas wrench.
- Next we remove the second oil seal.
Now it is necessary to prepare a place for the subsequent installation of the bearing assembly. Thoroughly clean the drum and tank with a cleaner and a rag. Then we wipe it dry and take out replacement parts.
Installation of new parts
All that remains is to change the bearings yourself. First, we take a ring with a smaller diameter, place the tank with the hole for the drum facing up and insert the part into the seat. We lower the chisel with a blunt base and tap it with a hammer in a circle until it shrinks completely. Then we install a suitable oil seal, lubricate it with a special compound and turn it over.
Next in line is the external bearing, which is mounted in a similar way: we place it in the hole and compact it with blows. After that, generously coat the shaft with lubricant and screw the drum into the tank. It would be a good idea to apply sealant to the bearing assembly.
Now we have to correctly reassemble it. We return the tank to its place and connect the two halves of the tank together with the previously unscrewed screws. At this stage, we recommend checking the quality of the work by turning the container left and right. If there is no extraneous noise, the installation is completed perfectly.
Next, we fix the pulley, tighten the counterweights, attach the heating element and connect the two removed sensors. Be extremely careful with the capillary one - the gas tube is easily damaged by the slightest pressure. At the “finish” you need to put on the drive belt and tighten both covers. Don’t forget to “run” the machine through a test wash, choosing the shortest mode.
Interesting:
Reader comments
- Share your opinion - leave a comment
Categories
Washing machine repair
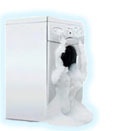
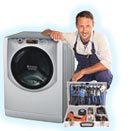
For buyers
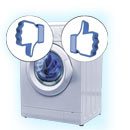
For users
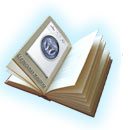
Dishwasher
Add a comment