Beko washing machine does not spin
If the cycle has ended, and there is water or completely wet clothes left in the drum, then there is only one conclusion - the washing machine does not spin. This kind of trouble often occurs with washing machines from VEKO, and it is not always a large-scale problem. Our article will help you understand what led to the failure, simple inattention or a serious problem. We will analyze possible sources of defective spinning and provide instructions for eliminating them.
List of possible problems
You shouldn't tolerate wet laundry. Finishing a thankless job with the washing machine is not only unpleasant and time-consuming, but what’s worse is that an unresolved breakdown can aggravate the problem to the point of a disastrous outcome. To know where to look for a problem, you need to understand the range of possible causes of a failed spin cycle. For Beko models we are talking about the following situations:
- No spin program selected;
- there is an imbalance in the drum;
- the drain does not function;
- the tachogenerator has failed;
- the electric motor broke down;
- drum bearings are worn out;
- the control board does not work;
- a foreign body has entered the tank, preventing the drum from spinning.
In 99% of cases, the problem that has arisen can be solved independently. The help of a professional repairman is only needed if the control module is burned out. All that remains is to correctly diagnose the source of the problem, for which it is enough to consistently check each possible option. Step-by-step instructions are given below.
Let's check the washing program
First of all, it is recommended to weed out trouble-free situations.Often there is no breakdown, since by mistake the user turns on a mode that does not involve intensive rotation of the drum. Thus, spinning is not provided for delicate washing and for wool, silk, and down programs.
To confirm your suspicions, you need to remember the selected button and read its description in the factory instructions. Next time, just change the mode or additionally turn on the spin cycle. The second thing we check is whether the spin cycle was accidentally canceled in the standard program.
Important! Don't forget to lock the dashboard, which will help you avoid worrying about accidental switching.
Many modern models allow you to vary the rotation speed of the drum up to its complete cancellation. It’s better to do a test: select a mode, set the push-up to maximum and start the machine again. Wet items will be a reason for further inspection.
Let's look at the laundry in the drum
The spin cycle of a Beko machine often does not work due to an imbalance in the drum. Overload, insufficient loading or uneven distribution of laundry along the walls of the tank leads to imbalance. This problem occurs with older models, since modern machines are equipped with a special function that controls the balance during washing and spinning.
It’s easy to suspect something is wrong: in this case, the unit repeatedly tries to spin up, but to no avail. As a result, the cycle ends 7-15 minutes earlier than the scheduled time, and the laundry remains wet. You can correct the situation as follows:
- Wait until the hatch is unlocked and open the door.
- Take out half of the laundry (if there was an overload), unravel the twisted “lump” or add items (if there is a shortage).
- Close the hatch tightly.
- Start spinning.
- Check the laundry for dryness.
Imbalance has a detrimental effect on the shock absorbers, bearing assembly and shaft, so it is best to avoid it. It is important to control the amount of laundry loaded and remember both the upper and lower limits. So, in a machine with a capacity of up to 5 kg, it is necessary to wash at least 1 kg, and in washing machines with a maximum capacity of 8-9 kg - 2.5 kg.
Waste water is not removed
If at the end of the cycle there are not only wet things in the drum, but also a full tank of water, you should pay attention to the drainage system. It is quite possible that the machine simply cannot drain the waste liquid due to a burnt-out pump, a blocked pump impeller, or a blockage in the hoses or pipes. We look for a specific cause and its solution in the following sequence:
- We disconnect the drain hose from the sewer and probe its length for blockages. If foreign objects are found, unscrew the pipe completely and rinse it under strong water pressure.
Attention! Sometimes the general sewer becomes clogged, so we lower the disconnected end of the drain hose into the sink or bathtub, start the drain or spin mode and wait for the water to flow.
- We find the drain hatch in the lower right corner of the washing machine body and, using a screwdriver, pry it open. We substitute a container for collecting water and unscrew the garbage filter. Clean the part and the fittings suitable for it. If everything is clean, we test the contacts with a multimeter.
- We check the integrity of the pump. We free the impeller from wound hair and fur, clean the pump body and measure the amount of resistance present.
The pump and filter cannot be repaired and, in case of breakdown, are replaced with new ones. After all the manipulations, we start the machine for the fastest wash and monitor the drainage of water.An empty drum will eliminate the fault of the drain system.
Hall sensor does not function
Spin does not work even if the tachogenerator is faulty. This device, also called a Hall sensor, is responsible for monitoring the number of revolutions made by the engine and transmitting information to the control board. If it breaks, communication with the module is lost, the system stops receiving information and, for safety reasons, reduces the motor power.
Breakdown is caused by improper operation of the machine, in particular:
- Regular overload of the machine with laundry.
- Prolonged use of the machine without stopping.
- Loose fastenings.
- Loose contacts or damaged wiring.
- Severe voltage surge or short circuit.
First of all, we inspect the wires and, if necessary, tighten the terminals, clean and insulate the conductors. Next, we call the sensor itself a multimeter and evaluate the results. In case of deviations from the norm, we replace it with an analogue.
The motor does not spin the drum
Another situation arises when the engine is not able to accelerate to the required power. For commutator motors, braking is possible when the electric brushes are worn out: washing and rinsing proceed normally, but spinning becomes impossible. If other stages of the cycle are difficult to complete, the engine itself may also break down. The guess is checked in the following way:
- We disconnect the machine from all communications.
- Unscrew the back cover.
- Remove the drive belt.
- We disconnect all connected places.
- Loosen the holding fasteners.
- We rock the motor and take it out of the grooves.
Next, wipe the body with a cloth and inspect for damage. A burnt-out engine has an unpleasant burning smell, stains and charred wires.Then we pay attention to the electric brushes: remove them from both sides of the engine, open them and measure the length of the tip. If it is less than 0.7 mm, you will have to change the pair to a new one. At the same time we call the coils.
Electronic unit malfunction
The worst thing is when the electronics fail. In this case, the triac responsible for spinning burns out, the engine does not receive a command to accelerate and is not able to accelerate the drum. Only a specialist can determine that the reason is in the module, so if you have the slightest suspicion, you should contact the service department.
It is not recommended to repair the module yourself. There is a high probability that a lack of experience, equipment and professionalism will result in the final failure of the board. A replacement part is expensive and it is cheaper to pay for the services of a specialist.
Foreign object in tank
A foreign object caught in the tank also prevents the drum from unwinding. Here it is necessary to react as quickly as possible: a foreign body can damage the walls of the containers and lead to jamming of the entire system. Replacing a tank is very expensive, so at the slightest suspicion it is recommended to stop the machine and remove the dangerous element.
It’s not easy to get a thing, and it’s better to first confirm the diagnosis. To do this, unplug the machine from the network, drain the water, open the hatch door and turn the drum in both directions. The resistance encountered clearly indicates an existing obstacle, so let's get down to business:
- We check that the unit is disconnected from the power supply.
- Turn off the water and disconnect the drain hose.
- We provide free access to the machine from all sides.
- Unscrew the bolts from the back and remove the back wall.
Important! Find out in advance in the instructions on which side the heating element is located in your VEKO model.
- Finding the location of the heating element.
- We take a photo of the heater so that we don’t mix up the wires when we return.
- Loosen the retaining bolts and remove the heating element.
- We insert our fingers or long-nose pliers into the vacant space and pull out the object that has fallen into the tank.
When the trouble has left the machine, it is worth carrying out an extraordinary cleaning for the heating element. Scrape its surface from scale and dirt, not forgetting to clean the contacts. Then we return everything to its place and test the rotation of the drum.
Bearing problems
You can suspect that a faulty bearing assembly is to blame for a poor-quality spin by the sounds emanating from the operating machine. Unusual noise, creaking, knocking indicate that the seals have served their seven-year life and have leaked, ruining the bearings with washed out grease and corrosion. It is impossible to return these elements to their factory condition - only replace both the bearings and seals with similar parts.
Here the instructions on what to do will not be short and simple. Firstly, it is necessary to find suitable replacement analogues, based on the serial number of the VEKO model. Secondly, disassemble almost the entire machine, right down to removing the counterweights and tank. Thirdly, carefully knock out the rusted rings without damaging the shaft and drum walls. Complicating the work is the lack of a special puller for an amateur repairman, as well as a number of other tools and consumables.
Before getting down to business, you should weigh all the pros and cons and decide exactly whether you have enough strength and experience for such work. There is a high probability of damaging the wiring, ruining the pipes or puncturing the tank. But it is worth taking into account the high cost of such repairs: on average, replacing a bearing assembly and seals costs a third of the price of a new washing machine.
But no one forbids you to first get to know the process in more detail and evaluate your strengths. The main thing is to carefully think through all the actions, prepare everything you need and enlist the help of an extra pair of hands. Step-by-step instructions for changing bearings yourself are given in this article.
Interesting:
Reader comments
- Share your opinion - leave a comment
Categories
Washing machine repair
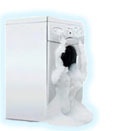
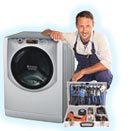
For buyers
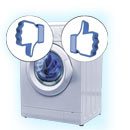
For users
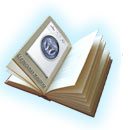
Dishwasher
Add a comment